Week in Review: Betrayal, Backdoor Deals & Billion-Dollar Blind Spots
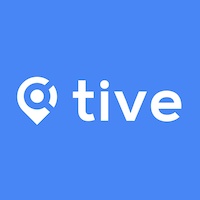
July 24, 2025
July 24, 2025
x min. Lesedauer
.jpg)
Welcome to another topsy-turvy week in the supply chain, where your employees are moonlighting as cargo thieves, the FDA’s “generous” extension is actually a competitive trap, and record heat is melting your pharmaceuticals on loading docks. This week, insider-assisted theft rings infiltrate warehouses, that 30-month FSMA extension might be a double-edged sword, 2025’s scorching temps turn drug shipments into expensive soup, and nearly half of companies can’t see their software supply chains—explaining those 80% hack rates. But at least LG Electronics managed to slash Scope 3 emissions by 20%, so perhaps there’s hope.
When Enemies Come From Within: Cargo Thieves Go Corporate
BSI Consulting’s second-quarter report (April 1 to June 25) reveals a troubling spike in insider-assisted cargo theft, especially in Miami and Los Angeles. Yet, despite the general surge in cargo theft (which shows no signs of slowing), Tony Pelli, BSI’s global director of supply chain resilience, still called the trend “a bit of a surprise.”
The Art of the Inside Job Gets an Upgrade
Criminals have gotten creative with their recruitment tactics. They’re bribing employees, phishing for warehouse details, and even corrupting truck drivers to spill shipping secrets. The “ant method”—stealing small amounts over time—lets thieves fly under the radar while organized groups run sophisticated fraud schemes. California has become the epicenter of this fraud-meets-theft hybrid, where criminals solicit insider information to execute strategic heists. That, in a nutshell, is why Pelli recommends cybersecurity training for all employees—so they learn to spot suspicious emails and recognize when someone’s fishing for confidential details.
By the Numbers: Where Thieves Strike Hardest
When it came to overall cargo theft trends, Mexico dominated Q2 2025 with a staggering 63% of North American incidents, leaving the U.S. at 32% and Canada at just 3%. Tractor-trailers bore the brunt with 85% of U.S. cases, led by truck hijackings (25%), vehicle thefts (19%), and facility break-ins (18%). Most crimes struck cargo in transit (39%) or in warehouses (22%), with thieves favoring food and beverages (23%), agricultural goods (15%), and automotive parts (9%). Pelli’s advice cuts straight to the point: slow down and verify carriers through FMCSA records—because when speed trumps security, your cargo pays the price.
FSMA 204: Why That 30-Month Extension Might Be Your Worst Enemy
In theory, the FDA just gifted food manufacturers with a potential 30-month extension to the January 20, 2026, FSMA Section 204 deadline. But not all is as good as it sounds. That extra time might be the very thing that sinks you.
Why “More Time” Means More Trouble
The FDA’s March 2025 extension gave food companies an extra 30 months on enhanced traceability requirements. Most immediately relaxed, while their smarter competitors doubled down on building real-time tracking systems. These companies are preparing for 24-hour recall responses and mastering critical tracking events, while others cling to the old way of doing things. That may prove to be a big mistake, because here’s what the extension doesn’t change: your soup still contains traceable tomatoes, your snack bars still need lot-level tracking for their ingredients back to the field, and global supply chain disarray is making ingredient sourcing messier by the day. The extra time is an opportunity—not a free pass.
The Reality Check
Thirty months sounds generous until you realize what needs to happen: mapping your entire supply chain to the farm level; establishing digital traceability workbenches in your ERP; killing those Excel logs forever; and training teams across procurement, production, and quality control. Run a mock recall right now. Can you trace every lot of ingredients from your last six months of production? If that takes more than a couple of hours, you’re proving the point. Companies that move fast will use this window to build competitive advantages—while everyone else panics at the new deadline. The clock is ticking.
Pharma Meets Furnace: How to Survive Scorching Weather
Your medications are melting—literally. 2025’s January-May global temperatures rank as the second warmest in 176 years of recordkeeping (2.25°F above the 20th century average of 55.5°F), and pharma companies face a scorching reality: extreme heat can destroy product integrity at the snap of a finger.
Handoff Heat: Where B2B Shipments Go to Sizzle
Pallet-load handoffs create pharmaceutical nightmares. Staging areas, tarmacs, and transfer facilities become temporary ovens where even brief temperature lapses compromise sensitive biologics, insulin, vaccines, and specialty injectables that must stay below 8°C (46°F). Room temperature pharmaceuticals—such as antibiotics, heart medications, and pain relievers—begin to degrade when ambient conditions spike above 86°F for extended periods. There’s a reason why smart shippers now think outside the box with tactics such as active temperature-controlled packaging and qualified passive thermal systems with insulated pallet shippers, gel packs, and phase-change materials.
Doorstep Disasters: Last-Mile Temperature Roulette
Direct-to-consumer shipping is also a wild card because when packages sit for hours in mailboxes, on porches, and inside delivery trucks, unpredictable exposure risks are created. Passive thermal protection now goes beyond basic insulation: reflective pallet covers and insulated containers maintain controlled room temperature stability for 48+ hours, even in 100°F+ ambient temperatures. Predictive delivery notifications help recipients retrieve parcels quickly, while temperature tracking via QR code scans builds consumer trust. Companies proactively adjust fulfillment centers and delivery methods during heat waves because many couriers can’t guarantee thermal control in transit—often visibility’s deepest black hole.
How Software Supply Chain Visibility Gaps Cost Companies Big Time
Companies are stumbling around in the dark when it comes to their software supply chains, and the numbers don’t lie. LevelBlue’s research reveals that 49% of organizations lack the visibility to fully understand or even identify their risks—a dangerous blind spot that’s leaving them wide open to attacks.
The Tale of Two Companies: 80% vs. 6%
The visibility divide creates a tale of cyber haves and have nots. Organizations with very low visibility suffer security breaches at an alarming rate: 80% experienced an attack in the past 12 months. Compare that to companies with very high visibility, where only 6% faced breaches. That’s not just a gap—it’s a chasm. You can’t protect what you can’t see, and companies flying blind are practically handing hackers the keys to the kingdom.
Risk Perception Goes Through the Roof
Not only does poor visibility increase actual risk, it also warps how companies perceive threats. A shocking 80% of low-visibility organizations view basic elements—such as custom code, commercial software, and API integrations—as very risky or somewhat risky. Meanwhile, 68% of organizations report that media attention has pushed cybersecurity up the C-suite agenda, yet only 25% plan to actually engage with software suppliers about security credentials in the next 12 months. Clearly, companies are worried—but they’re not yet walking the walk.
LG’s Carbon Diet: Slashing Scope 3 Emissions by 1/5
Korean electronics powerhouse LG Electronics is in the news this week because of how it not only cut Scope 3 emissions by nearly 20% since 2020 (led by AI and energy-saving tech), but exceeded expectations in the process.
Racing Past Deadlines
LG’s 2024 Scope 1 and 2 emissions came in at 910,000 tons of CO₂ equivalent. Now while that’s still somewhat higher than its 2030 target of 878,000 tons, the fact that it came this close with six years to spare is impressive. What’s more, LG set out to slash emissions by 54.6% compared to 2017 levels by decade’s end, then proceeded to flood its production processes with energy-efficient equipment and carbon-cutting tech. No wonder LG earned bragging rights as the first Korean home appliance company ever to receive a Science Based Targets initiative validation.
Turning Trash into Manufacturing Gold
LG crushed its waste game with a 97.4% recycling rate at production sites in 2024, handily beating its 95% target meant for 2030. Last year alone, LG hauled in 532,000 tons of used electronics from 91 locations across 56 countries. Its running total since 2006 now tops five million tons of collected appliances. LG also cranked up recycled plastic use by 36% year over year, proving that old gadgets make excellent building blocks for new ones. Dead refrigerators become tomorrow’s washing machines.
The Final Wake-Up Call
Whether it’s your own team stealing cargo, heat cooking your shipments, or hackers you can’t even see coming—this week’s disasters all have one thing in common: you can’t protect what you can’t see. Real-time shipment visibility is the difference between staying in business and becoming another cautionary tale, and at Tive, we see it time and time again.
Arm yourself with innovation: let Tive lead the way in transforming your supply chain operations. Embrace the future of logistics—get started with Tive today.