What Are Good Manufacturing Practices & GAMP-5 Compliance for Shipment Trackers? What Pharma Supply Chains Should Know
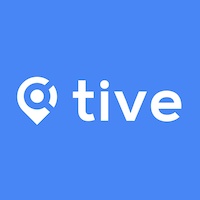
February 25, 2022
July 8, 2025
x min read
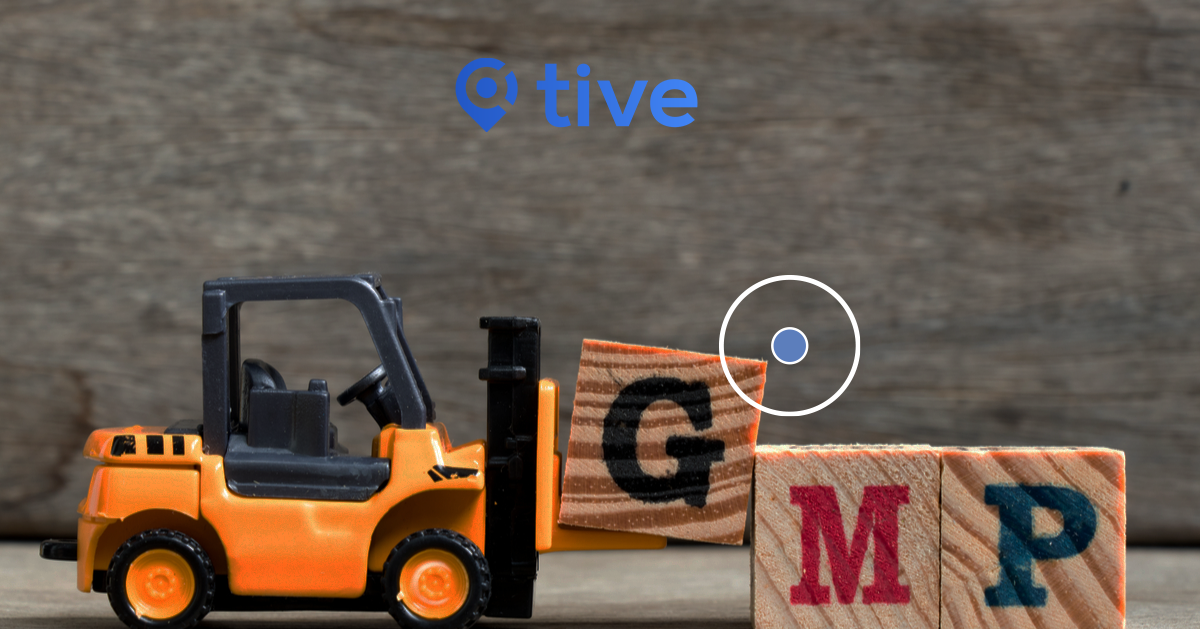
Good Manufacturing Practices (GMP) and Good Automated Manufacturing Practice Revision 5 (GAMP-5) standards are essential for pharmaceutical manufacturers to follow so they can meet regulations established by the U.S. Food and Drug Administration (FDA) and other regulatory bodies. Shipment tracking is part of the manufacturing cycle, and as such, GMP and GAMP-5 compliance is just as critical for this component as it is for other elements in pharmaceutical manufacturing.
What Are Good Manufacturing Practices?
GMP is a set of production standards that have been established for manufacturers in the food and drug industries to satisfy the needs and desires of regulators, retailers, and consumers.
GMP assures that a product was produced according to industry-established standards for:
- Buildings and facilities
- Equipment design and maintenance
- Sanitation conditions
- Employee practices
- Maintaining strong production controls
- Raw ingredient sourcing
- Records and reports
For the drug industry, the cGMP*(drug) standard addresses the production of pharmaceutical drugs for the United States (“cGMP” stands for Current Good Manufacturing Practices). The EU-GMP standard addresses production of pharmaceutical drugs for the European Union. Companies that want to address multiple markets have to consider all relevant standards (although many of the different standards are nearly identical).
According to the FDA, drug cGMP assures “the identity, strength, quality, and purity of drug products by requiring that manufacturers of medications adequately control manufacturing operations.”
What Is a Good Manufacturing Practices Certification?
To best market and sell their drug products, pharmaceutical manufacturers desire to have their products certified as being produced according to the applicable GMP. While certification isn’t necessary to sell products in all markets, obtaining a Good Manufacturing Practices certificate increases consumer and retailer confidence in a product dramatically and boosts a manufacturer’s reputation.
There are third-party audit firms that provide certification that manufacturers are following regulations set by the FDA and other regulatory bodies. Manufacturers must register with these bodies and follow all of the relevant regulations. Entire manufacturing facilities can be certified, but the process typically isn’t easy or quick. For manufacturers, there must be self-evaluations of standard operating procedures, comprehensive inspections of facilities by the FDA or other bodies, and GMP-related documentation.
Even after achieving certification, a manufacturer must continue to show its ongoing commitment to relevant cGMP.
What Is GAMP-5 Compliance?
Similar to GMP, which stands for Good Manufacturing Practices, GAMP is an acronym for Good Automated Manufacturing Practice, wherein “Automated” refers to computerized systems.
GAMP is most often used in relation to a guidance document titled GAMP-5: A Risk-Based Approach to Compliant GxP Computerized Systems (the “5” is the latest revision of the document, released in 2008). Published by the International Society of Pharmaceutical Engineering (ISPE), GAMP-5 is based on input from professionals within the pharmaceutical industry. It provides a framework for a risk-based approach to computer system validation. A system is evaluated and then assigned to a predefined category determined by its intended use and complexity.
Note that the strategies in the GAMP-5: A Risk-Based Approach to Compliant GxP Computerized Systems document are merely good manufacturing practices guidelines; they’re not regulations. Therefore, they don’t need to be followed. But the framework of the document provides a comprehensive approach to computer system validation that’s generally accepted within the pharmaceutical industry. Beyond that, its efficient risk-based approach is in line with the 21 CFR Part 11 and Annex 11 governing computer system validation application documents of the FDA and the European Medicines Agency (EMA), respectively.
GAMP-5 is also helpful in determining the scope of testing systems. Because ISPE also publishes reference materials specific to various systems requiring validation, manufacturers can use these guides when applying risk-based approaches to computerized systems.
Why Should Pharma Execs Care That Shipment Trackers Follow GMP & GAMP-5?
GAMP-5 and GMP-compliant manufacturing is vital for the pharmaceutical industry. In short, GMP and GAMP-5 help manufacturers meet regulations they must comply with to realistically sell in many target markets. These best practices are accepted, respected, and used by regulated companies and their suppliers globally.
Shipment tracking is often an automated service provided by systems integrators as a part of the manufacturing cycle; as with other parts of the cycle, the closer GMP and GAMP-5 are followed, the better off the manufacturer will be.
GMP allows data to be recorded by electronic data processing systems, but detailed descriptions of these methods must be provided, and the accuracy of all data needs to be verified. Data recorded by an electronic data processing system can only be modified or overwritten by authorized personnel.
Elements like timestamped, fully compliant digital e-signatures can be used as trustworthy, reliable, and equivalent alternatives to paper records to satisfy guidelines of the FDA and other regulatory bodies. Other elements can be made digital for more acceptable shipment visibility and traceability.
Following GAMP-5 and GMP manufacturing practices allows manufacturers to better control shipping exceptions, shortages, bottlenecks, critical orders, excess inventory, and potential delays; delays and deviations can be prevented, positively impacting end consumers. Where issues do occur, cross-process teams can understand how and why these transpire to prevent them from happening in the future.
The “Control Tower Model”
Using tools such as those available from cloud SaaS vendor Tive, the “supply chain control tower” model has arisen whereby a centralized hub uses data from existing platforms and integrates other systems, tools and processes across the supply chain to drive tangible business outcomes. This control tower model provides better shipment and overall visibility and allows manufacturers to discern real-time key performance indicators (KPIs) populated by data across an extended value chain. For the pharmaceutical industry, this control tower model provides six key benefits to supply chain members, including internal and external stakeholders:
- Visibility — Visibility, in this case, means real-time access to information across the complete supply chain. Internet-of-Things (IoT) data loggers travel with pharmaceutical products to ensure quality conditions are maintained and stakeholders can prevent lost loads.
- Automation — An exception-based quality release process singles out only problematic shipments that necessitate further review. Business and logistics processes will become more automated via workflow and communications processes.
- Analytics — Powerful analysis tools enable supply chain managers to make sense of visibility data, executing “what if”-type analyses to facilitate effective, rapid responses and root-cause analyses to drive operational and process improvements.
- Collaboration — Data is the currency of the future; it will enable enterprises to make decisions by connecting people and processes to work toward common goals. The recent vaccine distribution for the COVID-19 pandemic clearly demonstrated the need for greater responsiveness and collaboration throughout the supply chain.
- Responsiveness — By ensuring that each part of the supply chain is aware of the impact of the other segments, continuous improvement is enabled, and the ability to respond to issues before they escalate.
- Continuous Improvement — This can be achieved by working toward tangible KPIs using measured data. In this way, stakeholders can create action plans and respond to trends.
In the future, tools like Tive’s will allow for even more prescriptive analytics, data automation, machine learning, and artificial intelligence that will enable manufacturers to work in new ways. They will improve deliveries of drugs, drive better business outcomes, improve customer satisfaction and increase sustainability.
Conclusion
The pharmaceutical business is a very conservative industry based on many traditional methods and approaches, and there is much resistance to digitalization. Paper- and Excel-based verification and validation processes often use manual signatures. While these methods are “tried-and-true,” this approach has started to reach its limit — especially when there are multiple parties and subcontractors involved, these methods can be overwhelmed.
Meanwhile, expectations of consumers, retailers, and regulators are driving the industry toward technology-based solutions. The FDA and EMA have updated their regulations to describe electronic data and its handling.
The transportation component of the pharmaceutical supply chain is no different from other components, and it’s critical for manufacturers to adhere to regulations, have a good understanding of packaging, and have real-time shipment monitoring for observing temperatures and quality conditions. All of these will help manufacturers pass audits and satisfy the FDA, EMA, and other bodies, as well as please consumers, retailers, and other parties.
Read more Tive insights regarding pharmaceutical supply chains and end-to-end visibility.