Beyond Visibility: How to Build a Supply Chain That Thinks (White Paper)
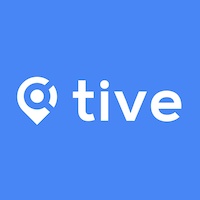
August 1, 2017
July 8, 2025
x min read
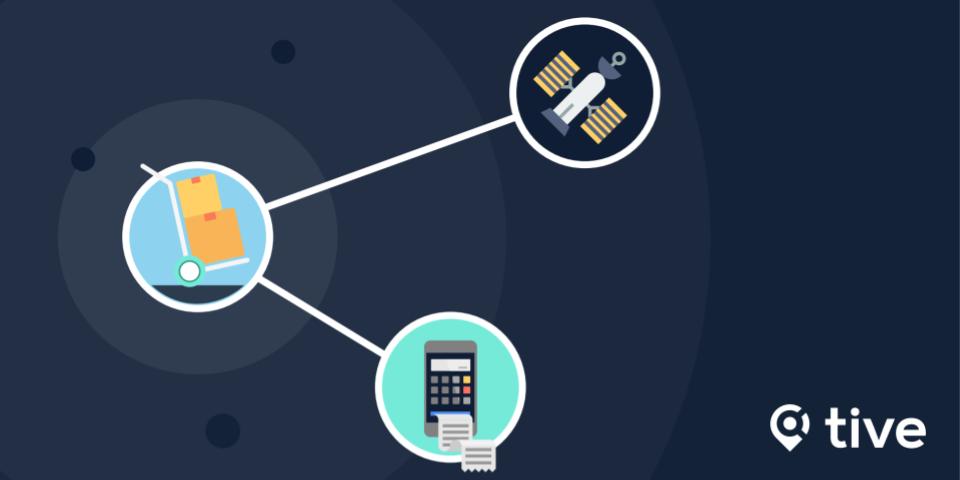
Abstract
Logistics managers have been waiting years for the next leap forward: end-to-end visibility. It is here, and it will give some organizations an unfair advantage on the field of global commerce. End-to-end visibility will bring about a cognitive, predictive and digital supply chain, in which the flow of goods, resources and people is mapped by an equivalent flow of information.
Introduction & Executive Summary
From the dawn of history to the shipping lanes of 2017, knowing the location of things has given some humans an edge. Anthropologists theorize that hunter-gatherers’ mental maps, which helped in the hunt, were also precursors to language and thought. From the pharoahs’ wealth to the British Navy, knowing where you are and where your stuff is has given some organizations an unfair advantage.
Napoleon Bonaparte was first to attempt to take that knowledge a step further. Semaphore, a line-of-sight telegraphy system, coupled location with near-instantaneous communication. At the height of Napoleon’s empire, a network of over 500 relay towers transmitted information across Europe via a visual code. Napoleon used his semaphore system to manage military logistics over longer distances than any other general of his time. You might say he was the first to attempt end-to-end supply chain visibility.
End-to-end visibility will bring about a cognitive, predictive and digital supply chain, in which the flow of goods, resources and people is mapped by an equivalent flow of information.
Two centuries later, logistics is making its next leap forward: end-to-end visibility. It is finally here, and it will give some organizations an imperial advantage on the field of global commerce. End-to-end visibility will bring about a cognitive, predictive and digital supply chain, in which the flow of goods, resources and people is mapped by an equivalent flow of information.
Today’s supply chains reach across the globe, and increasingly precise and persistent location data has enabled managers to run them lean, reducing waste and unnecessary inventory. After repeated hype cycles, end-to-end visibility has gone from simply a buzzword to an ever-elusive holy grail. But in 2017, a handful of technological advances have finally come together to make it possible for managers to track every component from its source to its arrival in the hands of the end consumer. More importantly, perhaps, the use cases are coming together that are making it easier for companies to see the benefit in sharing data up and down the extended supply chain.
New tracking technologies have filled gaps in supply chain visibility, while new information technology is capable of analyzing the torrent of data these tracking devices generate. In this white paper, we’ll explain how the combination of “big data” processing and better tracking devices can be used not only to monitor supply chain activity, but to identify and eliminate waste, pinpoint delivery times and predict failure points. End-to-end visibility is making a digital supply chain possible, enabling managers to apply Lean and Six Sigma methods in concert. The future of supply chain management is both predictive and cognitive.
A Brief History of End-to-End Visibility
The first supply-chain-visibility hype emerged in the 1990s, with the U.S. Army’s adoption of Radio Frequency Identification (RFID). It was a critical component of the movement tracking system (MTS), a system set up to supply Army units. The MTS was designed to enable quick re-routing of supplies based on emergent needs and changing conditions in the field. Every company supplying the Army was required to package its goods with RFID tags.
Wal-Mart soon followed suit from the private sector: in 2003, the massive retail chain announced a program to have all its suppliers tag pallets and cases with RFID transmitters. Its goal, end-to-end visibility, would represent a massive leap forward in Wal-Mart’s already vaunted logistical prowess. However, it didn’t work out that way: suppliers balked at the cost of the tags and Wal-Mart itself found its IT systems weren’t powerful enough to handle the massive amount of data. Wal-Mart abandoned its end-to-end visibility ambitions in 2009, just a couple years after the U.S. Army softened its RFID requirements for vendors.
New Technologies Are Enabling End-to-End Visibility
In the last few years, the cost of RFID has come down, and its uses are more prevalent. But it’s not the only tracking technology filling gaps in supply chain visibility. In fact, more expensive technologies like GPS (U.S.), GLONASS (Russian), Galileo (European), and Cellular (like GSM, WCDMA, LTE, and others) are part of the picture, according to the EU A.T. Kearney/WHU Logistics Study from 2015. In addition, cellular devices and services have become cheaper and less power-hungry. The other technology making end-to-end supply chain a possibility is improvement in low-power cellular connectivity, enabling sensor measurements to be transmitted to the cloud in real-time from almost anywhere on the globe, while consuming very little battery power. This allows many supply chain managers to gain insights into stretches of the supply chain where they did not have any visibility, and pull impressive amounts of working capital out of in-transit inventory.
It turns out the cost of implementing tracking devices isn’t the only obstacle preventing end-to-end visibility.
In addition to wireless connectivity improvements, sensor prices are coming down drastically, due to advances in micro electro mechanical systems (MEMS). These technologies have enabled miniaturization of sensors and proliferation of them in almost every device we carry around today. An iPhone 6S contains 10 different sensors; the iPhone 3G only contained three.
More important, perhaps, than the tracking technology, are the pieces of that puzzle that firms are implementing to get the most out of the information they’re tracking. That includes machine learning capable of multivariate regressions, predictive analytics and large-scale scenario analysis.
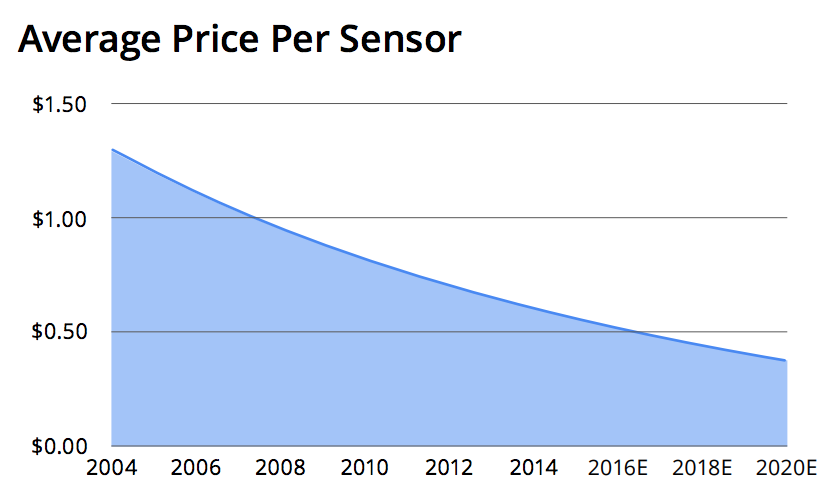
Source: Business Insider
It turns out the cost of implementing tracking devices isn’t the only obstacle preventing end-to-end visibility. As Wal-Mart learned a decade ago, supply chain tracking by any technology generates a large amount of data. Companies have to confront not only how to handle that data, but how to analyze it and draw actionable insights from it. Sometimes that involves not only reconfiguring how a company manages information about its supply chain, but re-imagining how it handles its supply and logistics and brings goods to market altogether. Now that end-to-end visibility is here, early adopters are realizing that this is where the challenge lies, and the opportunity.
How to Build Lean and Six Sigma into the “Cognitive Supply Chain”
End-to-end visibility isn’t an end unto itself. Once organizations can track the location of goods all the way up their supply chains, what can they do with the information?
The benefits begin with reducing lead times by automating processes and paperwork where human involvement can cause delay. A tracking device can communicate to customs officials about the contents of a shipment. A device can automatically let a warehouse manager know when a shipment enters a facility, removing the need for a human to check it in. This is a fairly tactical, event-driven use of the digital supply chain.
Beyond that is what Karl Kirschenhofer, Chief Operating Officer at Radio Frequency Systems, calls the “cognitive supply chain.” A cognitive supply chain is what happens when you take a digital supply chain and apply artificial intelligence.
“Most of the things we’re describing today means I’m looking into a database and I’m looking at a KPI,” said Kirschenhofer, who recently took over as COO at RFS, a designer and manufacturer of cable, antenna and tower systems, and radio frequency conditioning modules, based in Nozay, France. “This means it’s purely descriptive.”
A Six Sigma process that uses statistical analysis to predict failure points is “prescriptive,” he said, and it goes beyond the supply chain to the entire product life cycle. Applying machine learning to the data enables a supply chain system to learn from patterns in the torrent of data and extend them into the future, predicting when and where failure points are likely to occur.
A cognitive supply chain couples those Six Sigma predictive and preventative processes with a Lean Manufacturing view to eliminating waste in the supply chain. When an order comes in, the system immediately knows how the order is composed and which single component items the order is linked to. “I would know the housing number 3544, which has been ordered right now and is supposed to be delivered in 2 weeks, is already married and matched to that customer,” Kirschenhofer said. If housing number 3544 is damaged or delayed, the entire supply chain needs to be readjusted, he said. Downstream managers know that part is going to be delayed by one day and they adjust accordingly, or look for an alternative supply. The data from the digital supply chain makes it possible to pinpoint arrival date and make precise adjustments to eliminate waste.
Once organizations can track the location of goods all the way up their supply chains, what can they do with the information?
Exact timing of deliveries and precise awareness of delays will change the game in logistics, Kirschenhofer said. “[Today] you know that you’re expecting your product in six weeks,” he said, offering an example. Existing supply chain visibility technology may be enough to know it’s going to be late, but it’s very hard to get more precise than that. With current systems, “nobody will tell you that your items will arrive one or two days later,” Kirschenhofer said. Realtime sensor data on shipment location and condition allows companies to go further. A cognitive supply chain gathers sensor data about the shipment, analyzes that data and predicts that the part will be late, then triggers actions to mitigate the consequences of the delay, all without requiring human interaction. This is a supply chain that thinks for itself.
In addition to the efficiencies achieved using Lean and Six Sigma on the digital supply chain, an enterprise can become more responsive to its customers. It can implement a “demand-driven supply chain.” In some industries, such as fashion, this kind of insight has quickly grown from a competitive advantage to a survival necessity.
Exact timing of deliveries and precise awareness of delays will change the game in logistics.
“Obtaining real-time visibility across all tiers in the supply chain can significantly increase speed to market, reduce capital expenditures and manage risk,” Jeff Dobbs, global sector chair, Diversified Industrials at KPMG, told MEP Supply Chain. “Moving toward a demand-driven supply chain is probably the single most important step a global manufacturer can take today.” When implemented well, a demand-driven supply chain establishes a responsive flow of product all the way from the end customer up to the furthest upstream supplier. The demand-driven supply chain is more responsive to changes in customer behavior.
How Enterprises Are Turning Their Supply Chain Into Data
For those who aspire to broader visibility, integrating data from disparate sources is often the biggest hurdle. Manik Sharma, vice president of Kinaxis, a Canadian company making supply chain software, told Inbound Logistics that integration is a major hurdle for the company’s customers. “In most cases, they have data coming in, but they’re not able to connect that data,” he told the magazine. For example: “If I have a shipment and data coming in, the data has to reflect into the manufacturing plan so I can see what the impacts are, but often that connection does not exist”.
In other words, digitization is more than just adopting a tool or buying sensors. To achieve it, enterprises need to think through implications on various internal operations like shipping and receiving. An overwhelming majority of respondents in an A.T. Kearney/WHU survey said they expect major returns on forthcoming investments in IT integration, but challenges to integrating data abound. “Stovepipe solutions” and lack of trust between supply chain partners prevent the kind of data sharing that is needed to achieve a digital supply chain.
Digitization is more than just adopting a tool or buying sensors.
Some companies have implemented a “Supply Chain Control Tower,” overseeing collaborative processes, facilitating relationships between departments within the company and between companies in the supply chain, and implementing technology needed to share data. MEP Supply Chain outlined the three areas that have to change in order for the Supply Chain Control Tower strategy to work.
Processes: “Processes need to become more collaborative, with data sharing and planning being done across departments as well as between organizations.”
Relationships: “Information must be shared across processes not only within the organization, but within the functional silos such as planning, sourcing, production and delivery.”
Technology: “A major challenge in the sharing of information between tiers is the problem of passing data between disparate information systems.”
The Supply Chain Control Tower strategy, arching over multiple functions and processes, enables quick insight and action based on customer demand. Boston Consulting Group provides a brief case study: a global life-sciences company with $3 billion in revenue uses a control tower for replenishment and inventory planning “Depending on the pattern of customer clicks on the website in a country or region, a team member can adjust inventories even though customers have not yet placed orders. The company can also hold more stock in the right locations, which decreases the lead time promised to customers and increases their willingness to buy.”
Ultimately, companies need to eliminate local profit fiefdoms. Local profit centers optimize locally, often leading to sub-optimal corporate-level results. A digital supply chain manages local units as cost centers so that profit flows up to customer segments or products, supporting improved allocation and sharing of resources, Capgemini Consulting notes. Ernst & Young predicts firms that don’t go through these kinds of changes to establish a digital supply chain will be ill-equipped to benefit from coming waves of innovation in machine learning, Internet of Things (IoT) and blockchain.
Conclusion
It often happens that long-anticipated events turn out to have implications no one could foresee: This looks to be the case with end-to-end visibility as well. While Napoleon simply hoped to keep his troops provisioned, modern managers are finding that they can go beyond just getting product to the right place. The development of the digital supply chain, and eventually the cognitive supply chain, has implications beyond logistics and will touch every part of the modern enterprise. Like early humans building mental maps, companies that build the required capabilities in data capture, analysis, predictive modeling and organizational flexibility will continue to give their organization an unfair advantage.