Don’t Let These Bottlenecks Throttle Your Supply Chain
January 22, 2018
July 8, 2025
x min read
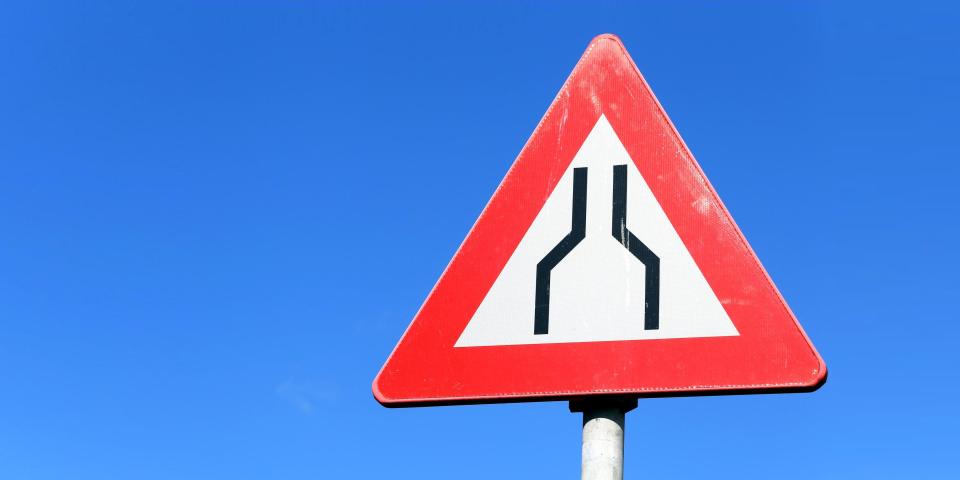
With new, high-tech solutions to gain real-time visibility into in-transit goods, the modern supply chain has become more optimized and efficient than ever before. But even with all that optimization, every supply chain is still subject to some major bottlenecks, and if those bottlenecks aren’t adequately accounted for and addressed, they can throttle your entire supply chain. Below we identify four key bottlenecks that face a global supply chain, and discuss the tools and strategies you can use to keep your supply chain running smoothly.
Airport Aggravations
For any supply chain that relies on air travel, airports are a significant bottleneck whose impact can ripple throughout the supply chain. While global cargo volumes continue to rise, airport infrastructure -- including everything from ground crew labor to taxiways and gates -- has struggled to keep up. The German Association for Freight Forwarding and Logistics has claimed that shippers relying on the major air cargo hub of Frankfurt often experience delays of over ten hours, dealing a crippling blow to their operations. Chicago O'Hare, a major U.S. hub, has experienced similar delays due to congestion and high shipment volumes. These unexpected delays lead to wasted labor hours as personnel wait for equipment to arrive, late product arrivals, and expensive expediting fees to make up the difference. Plus, if you’re paying for expensive air freight in the first place, it’s probably because your shipments are very time-sensitive -- so losing even just a few hours due to airport congestion can be a big deal.
Seaport Struggles
Seaports face many of the same obstacles as airports, and pose many similar challenges to supply chain managers. While ocean transit is relatively reliable, once cargo arrives in port, it can get stuck for days, weeks, or in some cases, years. This creates uncertainty and delays that trickle down through the entire supply chain. For example, this past December, cargo ships at several Chinese and Australian ports suffered extreme delays due to congestion and increased seasonal demand. One carrier reported 80 vessels waiting to enter port for over 20 days, while another waited six weeks before finally unloading at Dalrymple Bay port in Australia. These delays can be costly, unpredictable, and severely detrimental to the customer’s experience.
On the other side of the port, truck drivers entering port have sometimes wait up to eight hours to unload. One carrier reported that truck congestion at port was so severe that it cut the amount of goods their truckers could move each year by 50%, forcing the company to decrease profit margins and increase prices. Much of this congestion is due to ever-increasing global cargo volumes, and as shipping volumes continue to rise, this congestion and chaos at port will only get worse.
Trouble on the Tracks
In some ways, delays at an air or sea port are manageable (if annoying), since they are limited to a specific geographic location -- so once a shipment finally does port, you know the bottleneck is cleared. But if your shipment is travelling by train, clearing port doesn’t necessarily mean your troubles are over. In 2012, railway congestion was so bad that it took the average freight train 33 hours just to get from one side of Chicago to the other, adding more than a day to any shipment that went through America’s railroad hub. Delays in hub cities snowball across entire lines, causing widespread delays even in cities miles away from the original congestion.
Of course, it’s not just an American problem. European and Asian freight trains are also experiencing significant delays and congestion, up to six days for some routes, as freight volumes push past the capacity of railway systems. And it’s only going to get worse. Average freight transit times from LA to Chicago have increased by 70% since 2004, and the Association of American Railroads predicts that rail freight in Chicago will almost double by 2035, further straining the city’s already overstretched railway infrastructure. Meanwhile DB Schenker suggests that the number of containers traveling by rail between Asia and Europe will more than double by 2020, which will likely lead to further delays for international supply chains.
Bedlam at the Border
No matter what mode of transit you use, any global supply chain will face unavoidable bottlenecks at international border crossings. Anyone who has flown internationally is familiar with the long lines and bureaucracy that often accompany a border crossing, and it’s no better for freight. In Europe, for example, an analysis from Bain & Company suggested that supply chain disruptions due to Brexit could reduce manufacturers’ profits by 30%. Although some of this is due to anticipated frictions from new tax, labor, and immigration policies, delays in crossing borders and processing complex new customs paperwork are also likely to have a significant impact on the efficiency of European supply chains as they adapt to the new system. Meanwhile, in America, San Diego officials report that truckers entering the U.S. from Mexico often wait two hours to clear customs, and these delays lead to $6 billion in lost economic activity.
Beyond the Bottlenecks
The negative impact of these bottlenecks on a global supply chain is clear. But it can be less clear what to do about them. Some shippers have resorted to longer, less direct routes to avoid congested transit hubs. Other companies are proactively diversifying their supply chains with a variety of intermodal carriers, to lessen the impact of issues specific to rail, air, or sea travel. But ultimately, the way to combat costs associated with these systemic inefficiencies is through visibility. Specifically, awareness on a macro scale of technical and political developments that can influence these bottlenecks, as well as awareness on a micro scale of the location and ETA of your in-transit goods.
On the macro side, there are several recent developments and alternate solutions to be aware of. First, many of these bottlenecks could be mitigated with investment into port, road, and railway infrastructure. This is something that the U.S. government has long expressed interest in supporting. Former President Obama proposed a sweeping infrastructure investment bill back in 2010, and as recently as the spring of 2017, President Trump asked Congress to approve a $1 trillion investment into transportation infrastructure, promising that America’s “crumbling infrastructure will be replaced with new roads, bridges, tunnels, airports and railways.” Although details on these promised infrastructure plans are scant, in 2016 construction began on a 70-mile stretch of railway in San Diego that promises to significantly alleviate bottlenecks for freight traveling between the U.S. and Mexico.
Keeping tabs on projects like this can help supply chain managers stay ahead of the game. But staying up to date may involve following some unlikely news sources. Want the latest updates on how Brexit is impacting European supply chains? Consider joining an international supply chain group on LinkedIn, or subscribing to a Brexit-focused blog to get the latest news. Want to stay up to date on local infrastructure changes that may impact your business? Follow an airport or seaport on Twitter, such as the Port of LA or Chicago O’Hare Airport.
Real-Time Sensor-Driven Visibility
Of course, doing your research and reading the news will only get you so far. When it comes to gaining awareness about your specific shipments and how they may be impacted by these bottlenecks, a real-time tracking solution is the way to go. Real-time sensor-driven visibility solutions help companies gain awareness if a shipment has been delayed, enabling them to minimize disruptions by notifying customers, rescheduling labor, and ensuring safety stock is available in the right place at the right time. For example, a manufacturer shipping time-sensitive pharmaceutical products can put location trackers in the shipment and receive instant notifications if the package is delayed at en route or at port. Armed with this real-time visibility, the supply chain manager can take preemptive action to resolve any issues causing the delay and mitigate any fallout with customers or partners.
As with anything, knowledge is power. It is vital that supply chain managers take stock of the bottlenecks that impact their in-transit goods today, and ensure that they take appropriate measures to stay aware of relevant developments. That means staying on top of the latest technical and political developments relating to supply chain bottlenecks, as well as investing in a visibility solution to help work around delays and unpleasant surprises when they do occur. For more information about how real-time visibility can keep you prepared and in control, request a demo with Tive today.